热处理时间对不锈钢-碳钢爆炸复合板结合界面的影响
1 前言
在压力容器行业中,特别是一些用于化学工业的设备,由于长期在具有腐蚀性的环境中服役,因此对其制造材料的耐腐蚀性能有很高的要求。如果用单一的耐腐蚀材料进行制造,虽然满足了使用要求,但是大大提高了生产成本。可以考虑在保证材料强度和使用性能的前提下,通过在价格相对便宜的基板上复合一层耐腐蚀板材来达到降低成本的目的[1]。 本文以0Cr13不锈钢-Q235碳钢爆炸不锈钢复合板为试验对象,研究了不同热处理时长对其结合界面在组织形态、元素扩散及显微硬度等方面的影响,为确定合适的热处理时间提供了理论指导。
2 试验材料及方法
试验材料为不锈钢-碳钢爆炸不锈钢复合板,复层材料为0Cr13不锈钢,基层材料为Q235碳钢,厚度规格为3mm(0Cr13)+17mm(Q235),板材的化学成分如表1所示。从原始板材切取尺寸为25mm×10mm×20mm的3份样品,并将样品置于管式电阻炉中进行不同时长的热处理,试验方案如表2所示。处理后的样品用砂纸按照320#、400#、600#、800#的顺序依次打磨,最后用金刚石抛光膏进行机械抛光。考虑到不锈钢、碳钢两种金属耐腐蚀性能的差异,采用分次腐蚀的方法对样品进行化学腐蚀,碳钢一侧用的是4%的硝酸酒精溶液,腐蚀时间为5s,不锈钢一侧用的是5ml HNO3+50ml HCL+50ml H3O的混合溶液,腐蚀时间为8min。腐蚀后的样品用MR2000 型倒置光学显微镜进行金相组织观察,通过MH -3型自动数字显微硬度仪对界面结合区进行显微硬度的测定,并利用X射线能谱仪对试样界面区的元素扩散行为进行了分析。
3 试验结果及讨论
3.1 金相组织观察
图1a为焊态下不锈钢复合板结合界面区域的金相组织图。从图中可以发现,两种金属的结合界面呈现明显的波状特征,这是爆炸焊接工艺最显著的特点。碳钢一侧的组织为铁素体和珠光体, 由于爆炸产生的热效应使得界面附近的晶粒明显长大,晶粒尺寸随着远离界面而不断减小直到与基体晶粒一致。同时,界面附近的晶粒开始出现脱碳现象,碳从晶粒内部析出聚集于晶界。不锈钢一侧界面附近的晶粒呈现细长的纤维状,这是由于碰撞时剧烈的塑性变形促使晶粒沿着平行于界面的方向被拉长。图1b为2#试样结合界面区域的金相组织图。碳钢一侧界面附近的晶粒尺寸相对于焊态有所减小,这是在热处理作用下晶粒发生了回复再结晶。而焊态下聚集于晶界处的碳也因为热处理得以充分扩散,削弱了晶界处偏析作用的影响。不锈钢一侧界面附近的变形流线仍旧存在,但变形程度有所减小,晶粒开始有再结晶迹象。同时,碳化物数量明显增多,可能是碳钢中的碳扩散到不锈钢中与铬元素反应生成碳化铬,这将导致不锈钢中出现贫铬区域,降低了母材的抗腐蚀性能[4]。图1c为3#试样结合界面区域的金相组织图。碳钢一侧界面附近的晶粒开始长大,晶界处碳的偏析现象已经消失。不锈钢一侧的变形组织则进一步减少,分布于基体中的碳化物也基本消失,这是由于元素的扩散作用使得铬元素又重新固溶到母材之中,有利于提高材料的耐腐蚀性能。
3.2 结合界面SEM分析及X射线能谱分析
利用扫描电子显微镜对爆炸不锈钢复合板的结合界面进行了观察,发现不锈钢与碳钢之间存在两种结合方式,一种是直接结合(如图2a所示), 另一种是间接结合(如图2b所示)。间接结合方式中的中间层是由于基板和复板中的合金元素互溶形成的,该区域的化学成分介于复板和基板之间[5]。因为经历了金属熔化和凝固阶段,熔合层易出现气孔、裂纹等缺陷,成为界面结合较薄弱的区域。从图2中还可以发现,不管是以何种方式结合,界面附近都有超细晶粒带出现。这是在爆炸过程中由于材料的高速碰撞,在极短的时间内产生巨大的压力使该处金属受到很大的剪切作用,塑性剪切功转变的巨大热量使金属在很窄的区域内发生熔化,之后又急剧冷却,故形成极细的组织,甚至有非晶组织形成[6]。
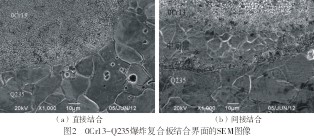
通过扫描电镜自带的X射线能谱仪对2#、3# 试样的基层金属,结合界面以及复层金属三个区域进行了分析,结果如图3所示,每个区域各主要元素的含量列于表3、表4之中。由试验数据可得,随着热处理时间的增加,界面两侧元素的相互扩散进行得更加充分,Q235中的Cr含量和0Cr13中的Mn、C含量显著上升[7]。在不锈钢一侧,长时间的热处理有助于碳化物的分解,使Cr元素重新固溶到母材之中,消除了贫铬现象对材料耐腐蚀性能的影响。同时,结合界面处由于热处理时间的增加导致碳化铬数量的增加, 脆硬的碳化铬提高了界面处的强度、硬度,但对其塑性、韧性有不利的影响。
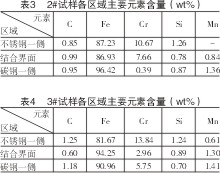
3.3 显微硬度的测定
利用MH-3型自动数字显微硬度仪对界面结合区的显微硬度分布情况进行了测定,试验数据如图4所示。由图可知,界面处的显微硬度明显高于两侧的基体金属,这是由于爆炸焊接过程中的高速碰撞使金属受到强烈的压缩作用和剧烈的塑性变形,从而导致在界面结合区产生不同程度的加工硬化。显微硬度随着与界面距离的增大而逐渐降低,当距离超过变形层的范围之后,硬度就趋近于基体金属的原始硬度了, 这主要是由于相应位置金属的塑性变形逐渐减弱所致。热处理时间越长,界面附近碳钢一侧的显微硬度相对于母材就下降得越剧烈。这是因为热处理有助于Q235中的碳扩散到界面和复层金属之中,导致此区域中形成了脱碳区[8]。同时,从两侧扩散而来的碳和铬促使界面处生成的碳化物不断增加,导致此处的显微硬度也随着热处理时间的增加而上升。
4 结束语
4.1 0Cr13-Q235复合板沿爆轰方向的界面呈明显的波状结合,且界面两侧的晶粒由于焊接过程中剧烈的碰撞都存在不同程度的变形。
4.2 不锈钢复合板进行热处理促使晶粒发生再结晶, 减少母材之中的变形组织,并有利于两侧金属之中的元素相互扩散,在界面处生成硬度很高的碳化物,提高了界面的结合强度。
4.3 随着热处理时间增加,界面两侧元素扩散进行得更充分。碳钢一侧出现脱碳区,不锈钢一侧则产生渗碳现象,且渗碳层中的碳化物呈网状分布或颗粒状分布。
4.4 在280℃进行热处理时,理想的保温时间是7小时。虽然界面邻近区域的硬度有所下降,但不锈钢中的碳化物发生了分解,使得Cr又重新固溶于母材之中,消除了贫铬现象对材料耐腐蚀性能的不利影响。
参考文献
[1] 郑远谋. 爆炸焊接和金属复合材料及其工程应用[M]. 长沙: 中南大学出版社. 2002.
[2] 王建明, 朱锡. 爆炸焊接的应用与发展[J]. 材料导报, 2006, 20(1): 42~45.
[3] 王克鸿,张德库,张文军. 爆炸焊接技术研究进展[J]. 机械制造与自动化, 2011, 40(2):1~4.
[4] 廖东波, 査五生, 李伟. 碳钢-不锈钢爆炸焊接复合板界面的显微结构[J]. 焊接学报, 2012, 33(5): 99~102.
[5] 史长根,王耀华,蔡立艮等. 爆炸焊接界面的结合机理[J]. 焊接学报, 2002, 23(2): 55~58.
[6] 张寿禄,王立新,裴海祥等. 不锈钢-钢爆炸复合板结合区组织的分析[J]. 特殊钢, 2003, 24(3): 13~16.
[7] 丁成钢,于启湛. 爆炸焊接复合板交界区的冶金行为[J]. 焊接学报, 2006, 27(1): 85~88.
[8] 王治平,何智,李强. 不锈钢/碳钢爆炸复合板消除应力热处理[J]. 高压物理学报, 1998, 12(1): 60~65.